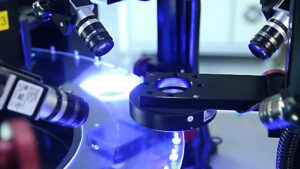
The electric connector manufacturer required an automation solution to complete the terminal assembling processing automatically, which is to replace the expensive labour, At the same time, improving the product quality. The automated crown spring terminal assembling machine provided by Xielitech, while designed with integrated functional test system.
The automated machine is capable of seamlessly integrating with various indexing structures, and each workstation on the index table performs efficient connector assembly, detection, and precise positioning functions, resulting in a highly optimized and streamlined process.
The machine has 12 workstations in total. The stations include loading, positioning, selecting spring direction, cutting carrier, assembling, detecting, pressing, CCD inspection, reject bad product, and outputting good finished parts.
The operator loads the brass barrels and springs into their respective vibratory bowls, and places a roll of ring clips onto the special loading system attached to the conveyor. This system is designed to efficiently transport the components to their next processing stage.
The vibratory bowl loading system for springs has been upgraded with a CCD inspection system to identify and eliminate defective springs, such as those that are twisted or misaligned. This ensures that only high-quality springs are conveyed to the next workstation, and that their orientation is strictly maintained. This optimization ensures smooth and efficient and production processes.
A rotary station with correct spring orientation has been incorporated onto the conveying platform to ensure that only springs with proper orientation are conveyed to the next working station.
A specialized cutting station for ring clips has been designed with a custom mold, cutter, and conveying structure. This station can produce two separated clips at once, which perfectly match the carrier structure.
Two workstations are currently listed on the index table in total. One is for detecting the clip. Once the clip is assembled onto the brass barrel, it undergoes a clip detection process using a photoelectric sensor at one of the workstations. The sensor is programmed to automatically turn off if no clip is detected on the brass barrel, and turn on when a clip is present. Another one is for detecting the spring and brass barrel. After completing the spring assembly, the CCD inspection system checks the coaxiality between the spring and brass barrel. It is crucial that the internal spring maintains full contact with the brass barrel to ensure stable current flow and guarantee the overall quality of the device. This meticulous process helps optimize the functionality and reliability of the product.
At the end of the automated production line, the rejection and output workstations have been integrated into a single station, resulting in significant reductions in machine size and cost. The rejection zone and finished goods zone, however, have been intentionally kept separate to ensure the highest level of product quality and to minimize the risk of contamination. This optimization strategy not only improves production efficiency, but also enhances product quality control and reduces overall costs.
Please provide us with your information and a brief description of your project. Our team will reply you within 8 hours.